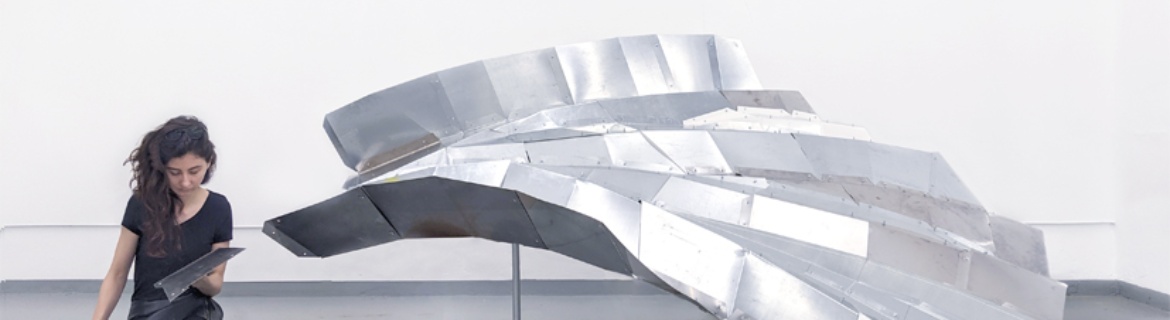
ITECH graduates Mobin Seyed Moussavi and Hana Svatoš-Ražnjević just published a journal article “Design based on availability: Generative design and robotic fabrication workflow for non-standardized sheet metal with variable properties” as part of the International Journal of Space Structures (IJSS) Special issue on Upcycling Spatial Structures with co-authors Axel Körner, Yasaman Tahouni, Achim Menges and Jan Knippers.
The article is based on their 2019 ITECH M.Sc. Thesis Project "Design Based on Availability". It presents the use of a computational design algorithm in combination with robotic fabrication and sensing to augment the design and construction process for non-standardized leftover sheet metal.
The article can be found at: https://doi.org/10.1177/09560599221081104
Congratulations Mobin and Hana!
Abstract:
This paper presents the use of a computational design algorithm in combination with robotic fabrication and sensing to augment the design and construction process for non-standardized material. Although reusing reclaimed material can significantly reduce the environmental impact in building construction, current design processes are not set up for this shift in thinking. Contrary to conventional practices, designing within the constraints of available material means that geometry and topology cannot be fully pre-determined. This paper introduces a design methodology for corrugated shell structures from folded sheet metal of variable geometries and properties, in which the design goal adapts to available material. It follows a two-fold approach of digital algorithm development and scanning and physical prototyping for robotic fabrication. The scanned materials database is classified based on object geometry data and material properties; such as thickness, type of metal, and spring-back values for fabrication purposes. Together with a target surface, it is an input for a generative design algorithm consisting of surface generation and optimization. The surface generation tries to approximate the target through a translation of search algorithm results for object placement into a 2D mesh graph which is then linked to 3D particle spring based form-finding. The optimization consists of evaluation of structural, fabrication, and design criteria, with finally user selection. Robotic fabrication included object recognition, metal sheet folding and consideration of different metal spring back behavior. These methods were tested on a single curved arch surface and applied to a double curved cantilever canopy as a final demonstrator. The algorithm results showed a generation of different corrugated shell topologies based on iterated object placement. As a demonstrator, a part of the selected canopy was robotically fabricated from local industrial leftovers.